Technologie/Dispositifs de fixation et d'assemblage mécanique/Calcul des assemblages par filetage
Une vis d'assemblage sert à effectuer un serrage, également appelé « flux bouclé[1] » ; du fait de cet effort de serrage, plusieurs sollicitations apparaissent dans le système vis-écrou. La forme de la vis et le filetage apportent de plus des concentrations de contraintes. Ainsi on doit prendre en compte le risque de ruine de la vis, qui peut soit casser ou simplement se déformer.
Situation | Mode de ruine et nature de la sollicitation |
---|---|
Section sous tête, noyau | arrachement des filets (cisaillement), rupture de la vis (traction) |
Surface d'appui | Compression, matage |
Sollicitations cycliques | Fatigue |
Notons que les vis sont utilisées dans d'autres cas que pour l'assemblage. Ces situations ne sont pas étudiées dans le présent chapitre, mais le tableau ci-dessous présente quelques aspects à prendre en compte.
Situation | Mode de ruine et nature de la sollicitation |
---|---|
Vis de pression | Cisaillement des filets : nombre de filets en prise en fonction du matériau Compression |
Vis d'arrêt | Cisaillement transversal : noyau ou section cisaillé |
Sollicitations cycliques | Fatigue |
Voir aussi le dossier Déformation élastique.
Caractéristiques géométriques des vis
[modifier | modifier le wikicode]Vis métal, profil ISO
Vocabulaire :
- diamètre nominal d : valeur (en mm) donnant son nom à la vis ; par exemple, le diamètre nominal d'une vis M5 est d = 5 mm ;
- pas P : longueur (mm) dont on avance lorsque l'on fait un tour de vis ;
- section résistante S : valeur (mm²) utilisée pour déterminer la résistance et l'allongement de la vis ;
- diamètre sur flanc d2 : diamètre (mm) au milieu du contact des filets, valeur retenue pour déterminer la frottement ; d2 = d – 0,649,5 × P ;
- diamètre de perçage D1 : diamètre (mm) auquel on perce un trou de vis avant taraudage, c'est aussi le diamètre intérieur d'un écrou ; D1 = d – 1,082,5 × P.
Diamètre nominal d (mm) |
Pas gros P (mm) |
Section de noyau S (mm²) |
Diamètre sur flanc d2 (mm) |
Diamètre de perçage D1 (mm) |
---|---|---|---|---|
1,6 | 0,35 | 1,08 | 1,373 | 1,221 |
2 | 0,4 | 1,79 | 1,740 | 1,567 |
2,5 | 0,45 | 2,98 | 2,208 | 2,013 |
3 | 0,5 | 4,47 | 2,675 | 2,459 |
4 | 0,7 | 7,75 | 3,545 | 3,242 |
5 | 0,8 | 12,7 | 4,480 | 4,134 |
6 | 1 | 17,9 | 5,350 | 4,918 |
8 | 1,25 | 32,9 | 7,188 | 6,647 |
10 | 1,5 | 52,3 | 9,026 | 8,376 |
12 | 1,75 | 76,2 | 10,863 | 10,106 |
16 | 2 | 144 | 14,701 | 13,835 |
20 | 2,5 | 225 | 18,376 | 17,294 |
24 | 3 | 324 | 22,051 | 20,752 |
30 | 3,5 | 519 | 27,727 | 26,211 |
Prétension et couple de serrage
[modifier | modifier le wikicode]
Lors de la mise en place d'une vis d'assemblage, il est primordial d'appliquer une prétension adaptée. Cette prétension permet de tenir les éléments en contact, et de compenser les efforts additionnels éventuels dus à des chocs, des vibrations, la pression, les sources de dilatation ou contraction — variations thermiques ou hygrométriques —, …
Pour les utilisations courantes, cela a peu d'importance. Mais lorsqu'il s'agit d'un assemblage étanche ou de sécurité, il faut maîtriser l'effort appliqué :
- trop faible, le système risque de présenter des fuites ou de se desserrer ;
- trop fort, on risque de détériorer les pièces, par exemple écraser le joint ce qui provoquera des fuites, ou bien de casser la vis.
La manière la plus simple d'avoir une prétension adaptée est de maîtriser le couple exercé sur la vis ou l'écrou : le couple de serrage. L'utilisation d'une clef dynamométrique est alors recommandée pour garantir la qualité du serrage.

Cependant, si cette méthode est simple à mettre en œuvre, on constate dans la pratique une grande dispersion dans la prétension réellement appliquée. Lorsque l'on désire maîtriser de manière plus précise la prétension, par exemple dans l'industrie nucléaire, on peut utiliser les méthodes suivantes :
- mettre la vis en traction avec une force donnée, visser l'écrou pour venir au contact sans jeu, puis relâcher la traction sur la vis ;
- chauffer la vis pour créer de la dilatation, visser l'écrou pour venir au contact sans jeu, puis laisser la vis reprendre ses dimensions en refroidissant ;
- mesurer la déformation élastique de la vis (torsion ou élongation) pour en déduire les efforts réels (respectivement couple de serrage et prétension).
Dans les trois cas, on élimine l'indétermination due à la dispersion des facteurs de frottement. Cependant, pour les deux premiers cas, cela nécessite d'estimer la partie de l'effort qui sert à déformer élastiquement les pièces à lier.
En pratique, pour des vis « métal » à filetage ISO, les règles de bonne pratique généralement admises sont :
- le concepteur détermine l'effort presseur que doit exercer sa vis ; il en déduit la résistance que doit avoir sa vis, ce qui détermine son diamètre d et la classe de qualité du métal[3] ;
- pour éviter le matage, dans le cas de forts couples de serrage (vis de qualité élevée), on répartit l'effort en utilisant des rondelles sous la tête de vis et sous l'écrou, ou bien des vis et écrous à embase tronconique (« H embase ») ;
- pour éviter l'arrachement des filets,
- dans le cas d'un boulon, l'écrou doit avoir la même classe que la vis : écrou classe 4 pour une vis classe 4.6 ou 4.8, écrou classe 10 pour une vis classe 10.9, … ;
- dans le cas d'un trou taraudé, la longueur engagée le de la vis doit être au minimum égale
- au diamètre nominal d pour un taraudage dans un métal « dur » (acier),
- à 1,5 × d pour un taraudage dans un métal tendre (alliage d'aluminium) ;
- le concepteur détermine ensuite le couple de serrage,
- soit à partir de l'effort minimum à appliquer pour assurer la fonction (cas d'un joint dont on veut éviter l'écrasement),
- soit à partir de l'effort maximum que peut supporter la vis (cas général).
Les fabricants donnent des tables d'application pour les vis et raccords les plus courants. Il s'agit cependant de la valeur limite à adopter avant endommagement de la vis. Il faut s'assurer que cela est supportable pour les éléments assemblés. Ce moyen est rapide et suffit dans la plupart des cas. Il faut bien prendre en compte l'état de surface et de lubrification du couple vis-écrou.
Pour certaines applications, comme par exemple le serrage d'une culasse de moteur thermique, il faut établir le serrage par paliers, souvent deux : un préserrage puis une mise définitive au couple.
Notons que pour des goujons, les longueurs d'engagement sont de 1,5 × d pour un matériau dur et 2 × d pour un matériau tendre.
d (mm) |
Classe de qualité | ||||
---|---|---|---|---|---|
3.6 | 4.6 | 8.8 | 10.9 | 14.9 | |
M3 | 0,38 | 0,46 | 1,23 | 1,74 | 2,43 |
M4 | 0,93 | 1,12 | 3 | 4,21 | 5,9 |
M5 | 1,81 | 2,17 | 5,79 | 8,15 | 11,4 |
M6 | 3,12 | 3,74 | 9,99 | 14 | 19,6 |
M8 | 7,43 | 8,92 | 23,7 | 33,4 | 46,8 |
M10 | 14,9 | 17,9 | 47,7 | 67,2 | 94,1 |
M12 | 25,3 | 30,4 | 81,1 | 114,1 | 159,8 |
M16 | 61,2 | 73,4 | 195,9 | 275,6 | 385,8 |
M20 | 119 | 143,2 | 382 | 537,1 | 752 |
d (mm) |
Classe de qualité | ||||
---|---|---|---|---|---|
3.6 | 4.6 | 8.8 | 10.9 | 14.9 | |
M3 | 0,679 | 0,906 | 2,41 | 3,40 | 4,75 |
M4 | 1,19 | 1,58 | 4,21 | 5,93 | 8,30 |
M5 | 1,91 | 2,55 | 6,81 | 9,57 | 13,4 |
M6 | 2,72 | 3,62 | 9,66 | 13,6 | 19,0 |
M8 | 4,94 | 6,59 | 17,6 | 24,7 | 34,6 |
M10 | 7,83 | 10,4 | 27,8 | 39,1 | 54,8 |
M12 | 11,4 | 15,2 | 40,5 | 56,9 | 79,6 |
M16 | 21,2 | 28,2 | 75,2 | 105,8 | 148 |
M20 | 33,1 | 44,1 | 118 | 165 | 231 |
Méthodes conventionnelles de détermination du couple de serrage
[modifier | modifier le wikicode]Formule de Kellermann et Klein
[modifier | modifier le wikicode]Kellermann et Klein[6] ont établi des formules semi-empiriques qui relient le couple de serrage C à la précontrainte Ft dans une vis, et qui ont servi de base à différentes normes :
- formule finale de Kellermann et Klein[7] : C = Ft·(0,161·P + 0,583·µt·d2 + 0,25·µh(Dext + Dint))
- norme ISO 16047 :
- forme de Motosh (1976)[8] :
- DIN 946 :
avec
- Ft : tension de la vis (ou précontrainte) en kN ;
- C : couple de serrage en Nm;
- P : pas de la vis ;
- Rh : rayon moyen sous tête (head) en mm ; Rh = (Dext + Dint)/4, avec
- Dext : diamètre extérieur de la tête de vis en mm,
- Dint : diamètre intérieur de rondelle ou de la surface frottante en mm;
- Dh : diamètre moyen sous tête en mm, Dh = 2Rh ;
- μh : coefficient de frottement sous tête ;
- r2 : rayon moyen du filetage, rayon sur flancs en mm;
- d2 : diamètre moyen du filetage, diamètre sur flancs en mm (Flankendurchmesser en allemand) ;
- μt : coefficient de frottement du filetage (thread).
Notons que ces formes sont grosso modo équivalentes :
- pour un filetage ISO, θ = 30° donc 1/cos θ ≈ 1,154 et 1/(2cos θ) ≈ 0,578 ; donc
- P/2/π + μtr2/cos θ ≈ 0,159 + 0,578 μtd2 ;
- dans la pratique, µt ≤ 0,25 et P << d2, donc
- 1,154·µt·P/d2 << π et ainsi
- .
Dans leur publication, Kellermann et Klein proposent de compenser l'élimination du membre 1,154·µt·P/d2 par une augmentation de 1 % des coefficients 1,154 et 0,578, ce qui donne les coefficients 1,161 et 0,583.
Du développement de la publication de Kellermann et Klein, on peut extraire une forme plus fondamentale :
où K est défini par :
avec
- µ't = tan φ't : coefficient de frottement apparent ;
- θ : angle de filet ;
- α : angle d'hélice au niveau de la ligne de contact supposée du filetage, lié au pas par la formule géométrique :
- .
On obtient ainsi la forme de Motosh :
Cette formule plus fondamentale permet par exemple d'évaluer l'intérêt d'utiliser un filet trapézoïdal standard (θ = 15 °) ou même un filet carré (θ = 0) : une application numérique montre que diminuer l'angle θ permet, par exemple, de diminuer le couple nécessaire pour créer un effort axial souhaité.
Notons que l'on peut aussi exprimer la formule dans l'autre sens :
Détermination simplifiée
[modifier | modifier le wikicode]Aux États-Unis, les ingénieurs utilisent souvent une relation simplifiée entre le couple de serrage et la prétension[9],[10] :
- C = K×D×Ft
ou K est le « facteur d'écrou » (nut factor) et D le diamètre de l'écrou. Le facteur K est établi par des essais. Cette approximation considère que le facteur K est indépendant du diamètre, et que l'on peut assimiler tous les diamètres (diamètre sur flanc, diamètre intérieur de l'écrou, …) au diamètre nominal. Une valeur donnée de K n'est valable que pour une gamme restreinte de vis ; K varie de l'ordre de 300 % si l'on considère toute la gamme de vis.

Dans des cas simples, on peut appliquer la méthode suivante.
Lors de la mise en tension de la vis, trois éléments constituent le couple de serrage :
- Le frottement du filetage
- Le frottement de la tête de vis (ou de l'écrou)
- La réaction à la tension induite par l'inclinaison du pas.
Nous ne tiendrons pas compte de la torsion de la partie filetée non en prise, de l'étirement différentiel le long du filetage en prise, …
Formules :
- M1 = Tension × µ × (Ømoyen filetage /2)
- M2 = Tension × µ × (Ømoyen appui /2)
- M3 = Tension × (Ømoyen filetage /2) × tan(α)
- Couple de serrage = M1 + M2 + M3
avec :
- Tension : effort à compenser pour une vis (en prenant tout en compte) ;
- Ømoyen appui : diamètre moyen la surface frottante ;
- α = angle du pas, soit arctan(P/(πרextérieur vis)) ;
- Ømoyen filetage = diamètre moyen du filetage (et pas le diamètre sur flanc) = (Øextérieur vis + Øintérieur écrou)/2 ;
- µ = coefficient de frottement (pour chaque surface) pour lequel il est admis :
µ | Conditions |
---|---|
µ = 0,10 | Lubrification adaptée et état de surface propre |
µ = 0,15 | Lubrification sommaire |
µ = 0,20 | Montage à sec |
Méthode VDI 2230
[modifier | modifier le wikicode]Choix de la vis
[modifier | modifier le wikicode]La recommandation VDI 2230 de l'Association des ingénieurs allemands (Verein Deutscher Ingenieure) utilise un tableau. La détermination se fait en quatre étapes :
- On détermine l'effort auquel doit être soumis l'assemblage. Dans la première colonne du tableau, on choisit l'effort immédiatement supérieur.
- Selon la manière dont est appliqué l'effort, on reste sur cette ligne — effort statique appliqué dans l'axe des vis — ou bien on descend de 1 à 4 lignes — 4 lignes dans le cas d'un effort transversal, tendant à faire glisser les pièces l'une par rapport à l'autre.
- Selon la manière dont est effectué le serrage, on reste sur cette ligne — cas où l'on contrôle le serrage par la déformation élastique de la vis à l'aide d'un dispositif électronique —, ou bien on descend de 1 ligne — serrage avec une clef dynamométrique — ou de 2 lignes — serrage avec une visseuse munie d'un limiteur de couple.
- La ligne ainsi définie donne les couples qualité de l'acier/diamètre nominal de la vis possibles.
Charge (N) |
Diamètre nominal (filetage ISO) | ||
---|---|---|---|
Classe de qualité de l'acier | |||
12.9 | 10.9 | 8.8 | |
250 | — | — | — |
400 | — | — | — |
630 | — | — | — |
1 000 | M3 | M3 | M3 |
1 600 | M3 | M3 | M3 |
2 500 | M3 | M3 | M4 |
4 000 | M4 | M4 | M5 |
6 300 | M4 | M5 | M6 |
10 000 | M5 | M6 | M8 |
16 000 | M6 | M8 | M10 |
25 000 | M8 | M10 | M12 |
40 000 | M10 | M12 | M14 |
63 000 | M12 | M14 | M16 |
100 000 | M16 | M18 | M20 |
160 000 | M20 | M22 | M24 |
250 000 | M24 | M27 | M30 |
400 000 | M30 | M33 | M36 |
630 000 | M36 | M39 | — |
Par exemple, un serrage doit empêcher deux plaques de glisser tangentiellement, sous un effort constant de 20 000 N :
- La valeur immédiatement supérieure est 25 000 N.
- C'est un effort transversal, il faut donc descendre de quatre lignes. L'effort presseur minimum est donc de 160 000 N.
- Le serrage sera effectué avec une clef dynamométrique. Il faut donc descendre d'une ligne, l'effort presseur maximum sera de 250 000 N, ce qui garantit, avec les différentes sources de dispersion, que l'on aura au moins un effort de 160 000 N.
- Les vis utilisables sont : M24 en qualité 12.9, M27 en qualité 10.9, ou M30 en qualité 8.8.
On remarque que, dans ce tableau, les charges suivent une suite géométrique de raison 1,6. Lorsque l'on descend d'une ligne, on ajoute donc 60 % à la valeur. La méthode VDI 2230 revient à estimer que :
- un effort alterné équivaut à un effort statique 60 % plus élevé ; la limite d'endurance à la fatigue d'un acier vaut 1/1,6 = 62,5 % de la limite élastique ;
- un effort normal excentré est équivalent à un effort normal centré 60 % supérieur ; le rapport des bras de levier est de 1,6 en faveur de l'effort excentré ;
- un effort tangentiel est équivalent à un effort normal centré 1,64 = 6,55 fois supérieur ; le coefficient d'adhérence vaut μ = 0,15 ;
- une clef dynamométrique a une précision de 60 % de la valeur nominale, et un limiteur de couple de visseuse une précision de 156 %.
Coefficient de serrage
[modifier | modifier le wikicode]D'après la formule de Kellermann et Klein, on voit que, pour un montage donné — triplet {diamètre, matériaux, lubrification} —, le couple de serrage et la précontrainte sont proportionnels ; graphiquement, la courbe représentative de Ft = ƒ(C) est une droite passant par 0. Le coefficient de proportionnalité — la pente de la droite — est appelé facteur de conversion X,
- C = X·Ft
et ce facteur dépend du pas P, des diamètres de la vis (diamètre sur flanc d2, diamètre moyen sous tête dh) et des coefficients de frottement μh et μt.
Les plus grandes sources d'erreur sont la valeur des coefficients de frottement et l'erreur de l'estimation du couple (erreur de mesure). Il faut donc majorer le couple visé, afin d'être sûr d'avoir le couple minimal requis, et donc la prétention minimale requise. On multiplie pour cela la valeur minimale par un coefficient de serrage αA, qui varie typiquement entre
- αA = 1,2 pour un serrage maîtrisant la déformation élastique de la vis, ce qui permet de s'affranchir du frottement : mise en prétention de la vis par traction, élongation par chauffage, mesure de la déformation élastique de la vis au serrage ;
et - αA = 4, pour un serrage avec une boulonneuse à chocs et à impulsion, le couple étant déterminé par le limiteur de couple de la boulonneuse.
Pour un serrage au couple avec une clef dynamométrique, on a typiquement un coefficient entre 1,6 et 2,5.
On peut diminuer ce coefficient en effectuant des essais pour déterminer avec précision le rapport entre la valeur mesurée du couple de serrage et la valeur réelle de la précontrainte.
Détermination du couple de serrage admissible
[modifier | modifier le wikicode]La recommandation VDI 2230 donne des valeurs maximales admissibles pour les couple de serrage et prétension, sous forme de tableaux semblables aux tableaux précédents (voir les tableaux Couples de serrage maximum admissibles (Nm) et Efforts presseurs maximum admissibles (N)). On se place à 90 % de la limite élastique (0,9×Rp 0,2) : le fait d'utiliser un coefficient de serrage permet de prendre une marge de sécurité plus réduite sur la valeur de la limite élastique.
Par ailleurs, le tableau distingue différents coefficients d'adhérence, pour des états de surface, traitements de surface et lubrification différents, mais estime que μh = μt. Il fournit également les facteurs de conversion X, ce qui permet de calculer facilement les couples de serrage minimum en fonction de la prétension.
d (mm) |
μ | Classe de qualité | ||||||
---|---|---|---|---|---|---|---|---|
3.6 | 4.6 | 5.6/4.8 | 6.8 | 8.8 | 10.9 | 12.9 | ||
M1,6 | 0,10 | 0,176 | 0,335 | 0,294 | 0,470 | 0,627 | 0,882 | 1,058 |
0,12 | 0,171 | 0,228 | 0,285 | 0,455 | 0,607 | 0,854 | 1,025 | |
0,14 | 0,165 | 0,220 | 0,275 | 0,441 | 0,588 | 0,826 | 0,992 | |
… | … | … | … | … | … | … | … | … |
M10 | 0,10 | 8,4 | 11,3 | 14,1 | 22,5 | 30,3 | 44,5 | 52,1 |
0,12 | 8,2 | 11,0 | 13,7 | 21,9 | 29,6 | 43,4 | 50,8 | |
0,14 | 8,0 | 10,7 | 13,3 | 21,3 | 28,8 | 42,2 | 49,4 | |
… | … | … | … | … | … | … | … | … |
M20 | 0,10 | 36,2 | 48,3 | 60,3 | 96,5 | 134 | 190 | 223 |
0,12 | 35,3 | 47,0 | 58,8 | 94,1 | 130 | 186 | 217 | |
0,14 | 34,3 | 45,8 | 57,2 | 91,6 | 127 | 181 | 212 | |
… | … | … | … | … | … | … | … | … |
M30 | 0,10 | 83,2 | 111,0 | 138,7 | 222,0 | 307 | 437 | 511 |
0,12 | 81,2 | 108,3 | 135,3 | 216,5 | 300 | 427 | 499 | |
0,14 | 79,0 | 105,3 | 131,7 | 210,8 | 292 | 416 | 487 | |
… | … | … | … | … | … | … | … | … |
M39 | 0,10 | 145,9 | 194,5 | 243,1 | 389,0 | 537 | 765 | 895 |
0,12 | 142,4 | 189,9 | 237,4 | 379,8 | 525 | 748 | 875 | |
0,14 | 138,8 | 185,0 | 231,3 | 370,0 | 512 | 729 | 853 |
d (mm) |
μ | Classe de qualité | X | ||||||
---|---|---|---|---|---|---|---|---|---|
3.6 | 4.6 | 5.6/4.8 | 6.8 | 8.8 | 10.9 | 12.9 | |||
M1,6 | 0,10 | 0,042 | 0,057 | 0,071 | 0,113 | 0,151 | 0,212 | 0,255 | 0,24 |
0,12 | 0,047 | 0,063 | 0,079 | 0,126 | 0,169 | 0,237 | 0,285 | 0,28 | |
0,14 | 0,052 | 0,069 | 0,087 | 0,139 | 0,185 | 0,260 | 0,312 | 0,32 | |
… | … | … | … | … | … | … | … | … | … |
M10 | 0,10 | 12 | 16,1 | 20,1 | 32,3 | 43 | 63 | 73 | 1,42 |
0,12 | 13,7 | 18,3 | 22,9 | 36,5 | 48 | 71 | 83 | 1,65 | |
0,14 | 15,2 | 20,3 | 25,3 | 40,6 | 54 | 79 | 93 | 1,89 | |
… | … | … | … | … | … | … | … | … | … |
M20 | 0,10 | 98 | 131 | 164 | 262 | 363 | 517 | 605 | 2,71 |
0,12 | 112 | 150 | 187 | 300 | 415 | 592 | 692 | 3,18 | |
0,14 | 125 | 167 | 209 | 334 | 464 | 661 | 773 | 3,65 | |
… | … | … | … | … | … | … | … | … | … |
M30 | 0,10 | 338 | 450 | 563 | 901 | 1 246 | 1 775 | 2 077 | 4,06 |
0,12 | 386 | 515 | 644 | 1 031 | 1 420 | 2 033 | 2 380 | 4,76 | |
0,14 | 431 | 575 | 719 | 1 151 | 1 597 | 2 274 | 2 662 | 5,46 | |
… | … | … | … | … | … | … | … | … | … |
M39 | 0,10 | 758 | 1 011 | 1 264 | 2 022 | 2 791 | 3 975 | 4 652 | 5,20 |
0,12 | 870 | 1 160 | 1 450 | 2 321 | 3 208 | 4 569 | 5 346 | 6,11 | |
0,14 | 974 | 1 299 | 1 624 | 2 598 | 3 597 | 5 123 | 5 994 | 7,02 |
Étude mécanique
[modifier | modifier le wikicode]L'assemblage vissé est un problème complexe, mais les éléments de base pour l'aborder sont relativement simples :
- géométrie élémentaire, en particulier la trigonométrie ;
- phénomènes d'adhérence et de frottement : loi de Coulomb (mécanique) ;
- statique du solide élémentaire, en particulier le principe fondamental de la statique ;
- résistance des matériaux, en particulier la traction.
Fonction de la vis
[modifier | modifier le wikicode]Le calcul doit se faire en fonction d'un cahier des charges ; il s'agit de faire un choix ou de valider une solution — une vis — en fonction de son utilisation.
La vis d'assemblage sert à effectuer un serrage, c'est-à-dire à maintenir deux pièces en position par adhérence. Nous excluons le cas des vis épaulées, qui assurent aussi une mise en position, voire servent d'axe de rotation, et l'utilisation des vis en aménagement d'intérieur (suspension d'objets).
Du point de vue de l'utilisateur, l'important est la force normale entre les pièces à lier, force exercée par l'ensemble vis/trou taraudé ou vis/écrou (boulon), notée Ft. Du point de vue du monteur, l'important est la force à laquelle il doit serrer : le couple de serrage, noté C. Tout ceci doit être déterminé par le concepteur, qui choisit une vis en fonction de sa résistance mécanique.
Maintien en position par adhérence
[modifier | modifier le wikicode]
Le maintien en position (MaP) par adhérence consiste à presser deux pièces l'une contre l'autre. Cet effort presseur est ici créé par une vis (et en général relayé par une rondelle).
Considérons une pièce liée à un support (pièce du bas dans le schéma ci-contre). La pièce est soumise à une action extérieure représentée par la force . La vis exerce un effort presseur . Le support exerce une action sur la pièce. La condition d'adhérence — de non-glissement de la pièce sur le support — peut s'exprimer de deux manières :
- géométrique : doit être à l'intérieur du cône d'adhérence, de demi-angle au sommet φa, où φa est l'angle d'adhérence ;
- analytique : se décompose en une composante normale et tangentielle , et l'on doit avoir
où μa est le coefficient d'adhérence entre les pièces à assembler ;
avec la relation
- μa = tan(φa).
Les coefficients μa et φa dépendent essentiellement de la nature des matériaux en contact et de l'état de lubrification.
Couple de matériaux | Non lubrifié | Lubrifié | ||
---|---|---|---|---|
μa | φa (°) | μa | φa (°) | |
Bois/bois | 0,65 | 33,0 | 0,2 | 11,3 |
Métal/bois | 0,5-0,6 | 26,6-31,0 | 0,1 | 5,71 |
Acier/fonte | 0,19 | 10,8 | 0,1 | 5,71 |
Acier/acier | 0,18 | 10,2 | 0,12 | 6,84 |
Acier/bronze | 0,11 | 6,28 | 0,1 | 5,71 |
- Pour plus de détails voir : Loi de Coulomb (mécanique).
L'action extérieure F1 est le « cahier des charges » : la liaison doit supporter un effort donné. Il faut donc choisir l'effort presseur F2 adapté. Dans le cas présent, la détermination est simple :
- F2 = F1/μa.
Mais cet effort presseur est la plupart du temps assuré par plusieurs vis ; il faut donc savoir comment se répartit cet effort.
Si le système est symétrique, on peut faire dans un premier temps l'hypothèse que l'effort est uniformément réparti : si l'on prévoit d'implanter n vis, alors chaque vis doit exercer un effort
- Ft = F2/n.
Si la pièce subit un moment de basculement (par exemple est en porte-à-faux), on peut supposer que l'effort varie de manière linéaire, et l'on dimensionne donc pour la vis la plus sollicitée. Dans les cas plus complexes, il faut avoir recours à un calcul par éléments finis ; on peut par exemple modéliser les vis par de simples poutres (éléments linéïques) pour connaître la sollicitation de chacune.
Géométrie de la vis
[modifier | modifier le wikicode]
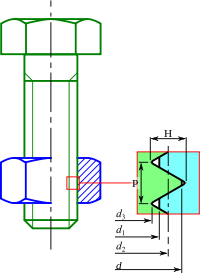
Le filetage et le taraudage ont des formes hélicoïdales. Si l'on considère une hélice d'axe vertical de diamètre d2 et de pas p, l'angle que fait la tangente avec l'horizontale vaut :
- .
Si l'angle est faible, ce qui est le cas pour les vis, alors on a en radians
- .
Le diamètre d2 à prendre en compte est le « diamètre sur flanc », c'est-à-dire celui de la « fibre neutre ». Dans le cas du profil métrique ISO, le profil du filet est grosso modo un triangle équilatéral, le rapport entre le pas p et la hauteur H du profil est donc de √3/2, soit H ≈ 0,866×p. On laisse 1⁄8H de jeu entre la pointe extérieure du profil et l'extrémité réelle du filet de la vis, soit
- d2 = d - 0,649,5×p.
où d est le diamètre nominal de la vis (diamètre extérieur du filet de la vis).
d (mm) |
p (mm) |
d2 (mm) |
α (°) |
d (mm) |
p (mm) |
d2 (mm) |
α (°) |
---|---|---|---|---|---|---|---|
M3 | 0,5 | 2,675 | 3,04 | M10 | 1,5 | 9,026 | 2,73 |
M4 | 0,7 | 3,545 | 3,19 | M12 | 1,75 | 10,863 | 2,66 |
M5 | 0,8 | 4,480 | 2,92 | M16 | 2 | 14,701 | 2,28 |
M6 | 1 | 5,350 | 3,04 | M20 | 2,5 | 18,376 | 2,28 |
M8 | 1,25 | 7,188 | 2,85 |
d (mm) |
p (mm) |
d2 (mm) |
α (°) |
d (mm) |
p (mm) |
d2 (mm) |
α (°) |
---|---|---|---|---|---|---|---|
M3×0,35 | 0,35 | 2,773 | 2,13 | M12×1 | 1 | 11,350 | 1,52 |
M4×0,5 | 0,5 | 3,675 | 2,28 | M12×1,25 | 1,25 | 11,188 | 1,90 |
M5×0,5 | 0,5 | 4,675 | 1,82 | M12×1,5 | 1,5 | 11,026 | 2,28 |
M6×0,75 | 0,75 | 5,513 | 2,28 | M16×1 | 1 | 15,350 | 1,14 |
M8×0,75 | 0,75 | 7,513 | 1,71 | M16×1,5 | 1,5 | 15,026 | 1,71 |
M8×1 | 1 | 7,350 | 2,28 | M20×1 | 1 | 19,350 | 0,912 |
M10×0,75 | 0,75 | 9,513 | 1,37 | M20×1,5 | 1,5 | 19,026 | 1,37 |
M10×1 | 1 | 9,350 | 1,82 | M20×2 | 2 | 18,701 | 1,82 |
M10×1,25 | 1,25 | 9,188 | 2,28 |
Dans le cas d'un filetage ISO à pas gros (pas par défaut), on a donc un angle d'hélice compris entre 2,28 et 3,19 °, et un rapport p/d compris entre 12,5 et 17,5 % du diamètre nominal, soit un rapport H/d compris entre 10,8 et 15,2 %.
Résistance de l'assemblage vissé
[modifier | modifier le wikicode]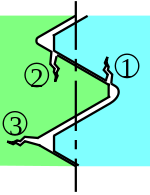
L'assemblage vissé présente quatre modes de ruine (voir figure ci-contre) :
- Arrachement du filet du taraudage ou de l'écrou (rupture en cisaillement).
- Arrachement du filet de la vis (rupture en cisaillement).
- Rupture de la vis (rupture en traction/torsion).
- Matage de la pièce sous la tête de vis (non représenté).
Résistance à l'arrachement des filets
[modifier | modifier le wikicode]Dans un premier temps, on peut évaluer le risque d'arrachement des filets.
Lorsque la charge augmente, les filets se déforment plastiquement, et la rupture est constatée sur tous les filets simultanément[11]. On prend donc en compte la totalité de la longueur engagée de la vis dans le taraudage :
- dans le cas d'un boulon, c'est la hauteur de l'écrou réduite des chanfreins : si un écrou a pour hauteur 0,8×d, la longueur utile Lu vaut 0,6×d ;
- et dans le cas d'un trou taraudé, c'est l'implantation j.

En considérant que la surface cisaillée est un cylindre « ajouré » :
- côté vis, la rupture a lieu sur le diamètre d1 (extrémité du filet de l'écrou) ; pour une vis ISO, d1 = d - 1,0825×p, la hauteur cisaillée étant les 3/4 de la hauteur totale ;
- côté écrou ou taraudage, la rupture a lieu sur un cylindre de diamètre d (diamètre nominal) ; pour un filetage ISO, la hauteur cisaillée est les 7/8 de la hauteur totale.
Si la vis est en prise sur une longueur le (longueur engagée), alors les surfaces résistantes des filets ont pour aire :
- côté vis : Afv = 3⁄4×π×d1×le
- côté écrou : Afe = 7⁄8×π×d×le
On peut donner une expression plus générale[12] :
le/p est donc le nombre de tours d'engagement. Pour un filetage ISO, θ = 30 °.
d | Afv/le (mm²) |
Afe/le (mm²) |
d | Afv/le (mm²) |
Afe/le (mm²) |
---|---|---|---|---|---|
M3 | 5,79 | 8,25 | M10 | 19,74 | 27,49 |
M4 | 7,64 | 11,00 | M12 | 23,81 | 32,99 |
M5 | 9,74 | 13,74 | M16 | 32,60 | 43,98 |
M6 | 11,59 | 16,49 | M20 | 40,75 | 54,98 |
M8 | 15,66 | 21,99 |
d | Afv/le (mm²) |
Afe/le (mm²) |
d | Afv/le (mm²) |
Afe/le (mm²) |
---|---|---|---|---|---|
M3×0,35 | 6,18 | 8,25 | M12×1 | 25,72 | 32,99 |
M4×0,5 | 8,15 | 11,00 | M12×1,25 | 25,09 | 32,99 |
M5×0,5 | 10,51 | 13,74 | M12×1,5 | 24,45 | 32,99 |
M6×0,75 | 12,22 | 16,49 | M16×1 | 35,15 | 43,98 |
M8×0,75 | 16,94 | 21,99 | M16×1,5 | 33,87 | 43,98 |
M8×1 | 16,30 | 21,99 | M20×1 | 44,57 | 54,98 |
M10×0,75 | 21,65 | 27,49 | M20×1,5 | 43,30 | 54,98 |
M10×1 | 21,01 | 27,49 | M20×2 | 42,02 | 54,98 |
M10×1,25 | 20,37 | 27,49 |
On voit que
- la surface résistante du taraudage est supérieure à la surface résistante de la vis, d'un facteur 1,3 à 1,5 : le diamètre du cylindre est plus important, et la hauteur également ; pour un même matériau, c'est le filetage qui va céder en premier ;
- un pas fin augmente la section résistante pour la vis, mais ne change rien pour le taraudage ; par contre, le montage d'une vis à pas fin est plus difficile, et l'on a plus de risque d'abimer le filetage.
La résistance au cisaillement de la matière est appelée Reg. La force ultime que l'on peut appliquer vaut alors
- Ft = min(Fv, Fe)
avec
- résistance du filet de la vis : Fv = k×Afv×Reg v ;
- résistance du filet de l'écrou : Fe = k×Afe×Reg e ;
le coefficient k est un coefficient de sécurité, pris habituellement égal à 0,9 ou à 0,75.
Matériau | Reg (MPa) | Matériau | Reg (MPa) |
---|---|---|---|
Alliage d'aluminium EN AB 21000 (A-U5GT) |
100 | Fonte EN GJS 400-15 (FGS 400-15) |
192 |
Alliage d'aluminium EN AW 2017 (A-U4G) |
120 | Vis classe 4.6 | 168 |
Acier S235 |
117 | Vis classe 8.8 | 512 |
Alliage d'aluminium EN AW 7075 (A-Z5GU) |
220 | Vis classe 10.9 | 720 |
De manière générale :
- pour un acier doux (S235, vis de classe 3.6) ou un alliage d'aluminium, Reg = 0,5×Re ;
- pour un acier mi-dur (vis de classe 4.6 à 6.8), Reg = 0,7×Re ;
- pour un acier trempé (classe 6.9 et supérieure) ou une fonte : Reg = 0,8×Re.
- Pour plus de détails voir : Cisaillement.
Dans la pratique, on détermine plutôt la longueur d'implantation le minimale, le nombre de filet minimum qu'il faut engager, pour une force de traction Ft. Plus la vis est implantée, plus la surface cisaillée augmente. On a à la limite :
- résistance du filet de la vis : Afv = Ft/k/Reg v ;
- résistance du filet de l'écrou : Afe = Ft/k/Reg e ;
soit
- vis :
- écrou :
Résistance à la traction de la vis
[modifier | modifier le wikicode]Une vis présente une section variant de manière brusque. On ne peut donc pas la modéliser par une poutre au sens strict. On définit cependant de manière conventionnelle un cylindre lisse ayant la même résistance. Son diamètre est appelé d0, et il est défini, pour le profil ISO, par
- d0 = (d2 + d3)/2
avec
- d2 = d - 0,649,5×p ;
- d3 = d - 1,226,8×p ;
soit
- d0 = d - 0,938,2×p.
Cela permet de définir une section équivalente de résistance en traction :
- Seq = π×d02/4.
d | d0 (mm) |
Seq (mm2) |
d | d0 (mm) |
Seq (mm2) |
---|---|---|---|---|---|
M3 | 2,484 | 5.03 | M10 | 8,593 | 58,0 |
M4 | 3,343 | 8,78 | M12 | 10,358 | 84,3 |
M5 | 4,249 | 14,2 | M16 | 14,124 | 157 |
M6 | 5,062 | 20,1 | M20 | 17,655 | 245 |
M8 | 6,827 | 36,6 |
d | d0 (mm) |
Seq (mm2) |
d | d0 (mm) |
Seq (mm2) |
---|---|---|---|---|---|
M3×0,35 | 2,671 | 5,61 | M12×1 | 11,062 | 96,1 |
M4×0,5 | 3,531 | 9,79 | M12×1,25 | 10,827 | 92,1 |
M5×0,5 | 4,531 | 16,1 | M12×1,5 | 10,593 | 88,1 |
M6×0,75 | 5,296 | 22,0 | M16×1 | 15,062 | 178 |
M8×0,75 | 7,296 | 41,8 | M16×1,5 | 14,593 | 167 |
M8×1 | 7,062 | 39,2 | M20×1 | 19,062 | 285 |
M10×0,75 | 9,296 | 67,9 | M20×1,5 | 18,593 | 272 |
M10×1 | 9,062 | 64,5 | M20×2 | 18.124 | 258 |
M10×1,25 | 8,827 | 61,2 |
La force ultime à laquelle la vis peut résister en traction est donnée par
- Ft = k×Seq×Re
où Re est la limite d'élasticité et k est un coefficient de sécurité.
Dans le cas de vis en acier non-inoxydable, la résistance de l'acier est donnée par une « classe », typiquement « 4.6 », « 8.8 » ou « 10.9 ». Le premier nombre indique la résistance à la traction Rm en centaine de mégapascals et le second nombre indique la proportion que représente la limite d'élasticité Re en dizaine de pourcent ; ainsi, un acier de « classe 4.6 » a un Rm = 400 MPa et un Re valant 60 % du Rm, soit Re = 0,6 × 400 = 240 MPa.
Matériau | Re (MPa) | Matériau | Re (MPa) |
---|---|---|---|
Alliage d'aluminium EN AB 21000 (A-U5GT) |
200 | Fonte EN GJS 400-15 (FGS 400-15) |
240 |
Alliage d'aluminium EN AW 2017 (A-U4G) |
240 | Vis classe 4.6 | 240 |
Acier S235 |
235 | Vis classe 8.8 | 640 |
Alliage d'aluminium EN AW 7075 (A-Z5GU) |
440 | Vis classe 10.9 | 900 |
Vis inox | |||
Nuances A1 à A5 classe 50 |
210 | Nuance C3 classe 80 |
640 |
Nuances A1 à A5 classe 70 |
450 | Nuance C4 classe 50 |
250 |
Nuances A1 à A5 classe 80 |
600 | Nuance C4 classe 70 |
410 |
Nuance C1 classe 50 |
250 | Nuance F1 classe 45 |
250 |
Nuance C1 classe 70 |
410 | Nuance F1 classe 60 |
410 |
Nuance C1 classe 110 |
820 |
- Pour plus de détails voir : Essai de traction.
Longueur d'implantation minimale
[modifier | modifier le wikicode]Comme indiqué précédemment, plus la longueur d'implantation est importante, plus la résistance au cisaillement du filet est importante. À partir d'une certaine longueur, les filets sont plus résistants que le noyau de la vis, c'est systématiquement la vis qui casse en traction.
On peut estimer cette longueur en introduisant la force ultime en traction dans la formule de la longueur résistant au cisaillement :
- côté vis :
- côté écrou :
soit
- côté vis :
- côté écrou :
En faisant les approximations d0 ≈ d et Re v/Reg i ≈ 2 (vis et taraudage en acier doux, par exemple boulon de classe 4), on a
- côté vis : le = 2d/3 = 0,667d
- côté écrou : le = 4d/7 = 0,571d
En supposant une vis de classe 8.8 (Re v/Reg v = 1,25) et un taraudage dans un alliage d'aluminium 2017 (Re v/Reg e = 5,333) :
- côté vis : le = 1,25d/3 = 0,417d
- côté écrou : le = 10,667d/7 = 1,524d
Ceci justifie les règles empiriques le ≥ d ou 1,5d.
Matage sous tête
[modifier | modifier le wikicode]Si l'on serre directement avec la vis ou l'écrou sur le plat de la pièce, la surface de contact a la forme d'un anneau. Le diamètre intérieur di de cet anneau est le diamètre de perçage d1, et le diamètre extérieur de est donné par la forme de la tête de vis. L'aire de cette surface sous tête vaut :
- St = π×(de2 - di2)/4.
La pression de contact vaut donc :
- P = F/St.
d | Forme de la tête | ||
---|---|---|---|
vis ou écrou H[13] | vis CHC[14] | vis ou écrou H à embase[15] | |
M5 | 6,9 | 8,03 | 9,8 |
M6 | 8,9 | 9,38 | 12,2 |
M8 | 11,6 | 12,33 | 15,8 |
M10 | 14,6 | 15,33 | 19,6 |
M12 | 16,6 | 17,23 | 23,8 |
M16 | 22,5 | 23,17 | 31,9 |
M20 | 28,2/27,7[16] | 28,87 | 39,9 |
La pression admissible dépend du matériau, mais il est difficile d'avoir des données. Pour les aciers de construction, on retient en général Padm = 200 MPa. Guillot propose lui des valeurs bien plus élevées (« avec une bonne sécurité »)[17] :
- Pmax = (Rec + Rmc)/2
avec
- Rec : limite élastique minimale en compression ;
- Rmc : résistance minimale en compression ;
pour les matériaux isotropes (la plupart des métaux non frittés, excepté les fontes), on prend Rec ≈ Rp0,2 et Rmc ≈ Rm.
Matériau | Rec (MPa) |
Rmc (MPa) |
Pmax (MPa) |
---|---|---|---|
Acier S235 (E24) | 235 | 340 | 288 |
Fonte EN GJS-400-12 (FGS 400.12) | 280 | 700 | 490 |
Alu EN AC-21000 (AU5GT) | 200 | 330 | 235 |
Alu EN AW-2017 (AU4G) | 240 | 390 | 315 |
Outre la détérioration de la pièce, le matage diminue la précontrainte, le serrage. Pour éviter ce phénomène, on réduit la pression de matage en utilisant des rondelles. Ceci est particulièrement important lorsque l'on utilise des qualités de vis élevées — donc pour des couples de serrage important — avec des matériaux de construction standard (aciers S235, S355, inox, alliages d'aluminium, …).
Relation entre la force de traction et le couple de serrage
[modifier | modifier le wikicode]Adhérence sur le filet
[modifier | modifier le wikicode]
Localement, la situation de la vis qui tourne dans le taraudage est semblable à un solide glissant sur un plan incliné. On appelle la force d'action locale du taraudage sur la vis.
On se place à un endroit du filet et on définit un repère cylindrique local, l'hélice étant inscrite dans le cylindre : l'axe x est radial, l'axe y est tangentiel et l'axe z est l'axe du cylindre. Si l'on développe l'hélice, le plan développé est le plan (y, z ).
Il n'y a pas de glissement « radial » (dans le plan (z, x )), donc la force est dans un plan incliné de l'angle θ = 30 °, l'angle du profil du filet, par rapport à z. À la limite du glissement, l'action de contact du taraudage sur la vis se situe sur le cône d'adhérence, donc fait un angle φ avec la normale au plan de glissement ; on a :
- φ = arctan(μ)
où μ est le coefficient d'adhérence.
Pour un contact acier-acier, on a typiquement μ = 0,18 (non lubrifié) ou 0,12 (lubrifié), donc φ = 10,2 ° (non lubrifié) ou 6,84 ° (lubrifié). Mais les coefficients présentent une grande variabilité : selon le traitement de surface (en général traitement anti-corrosion), la lubrification, mais aussi une grande dispersion pour des conditions données.
Traitement de surface | μ (φ) | |||
---|---|---|---|---|
Vis | Écrou | Non lubrifié | Huilé | Graissé au MoS2 |
Phosphatée | Aucun | 0,14-0,21 (7,97-11,9°) |
0,14-0,17 (7,97-9,65°) |
0,10-0,11 (5,71-6,28°) |
Galvanisé 8 μm (électrozingué) |
aucun | 0,13-0,18 (7,41-10,2°) |
0,13-0,17 (7,41-9,65°) |
|
Galvanisé 5 μm | 0,13-0,18 (7,41-10,2°) |
0,14-0,19 (7,97-10,8°) |
||
Cadmié 7 μm | aucun | 0,08-0,12 (4,57-6,84°) |
0,08-0,11 (4,57-6,28°) |
|
Cadmié 7 μm | 0,08-0,12 (4,57-6,84°) |
0,10-0,15 (5,71-8,53°) |
La force peut ensuite se décomposer en :
- une composante axiale Ft, qui met la vis en traction ;
- une composante horizontale Fc, qui produit un couple résistant.
On se place au milieu du filet, donc au diamètre sur flanc d2. On a donc :
- Ft = F×cos(α ± φ)×cos(θ)
Le moment de la force par rapport à l'axe vaut
Ce moment M1 est une composante du couple de serrage. On peut éliminer F pour mettre en relation Ft et M1 (en scalaire) :
- [19].
soit, en prenant α = 2,7 °, θ = 30 ° et φ = 6,84 ° (filetage ISO, pas gros, acier sur acier), en valeur absolue :
- M1 ≈ 0,0970×Ft×d (serrage)
ou
- M1 ≈ 0,0418×Ft×d (desserrage).
On a la relation trigonométrique suivante :
avec tan α = p/(πd2) et tan φ = μ. Par ailleurs, comme φ < 10° et α ≤ 2,28°, on a tan(α)tan(φ) < 0,008 qui est négligeable devant 1, soit
et donc :
- .
Le signe est positif au vissage et négatif au dévissage. Pour le vissage avec un filetage ISO, on a donc :
- M1 ≈ (0,184×p + 0,577×μ×d2)×Ft.
Exemple
Considérons une vis M10 à pas gros p = 1,5 mm = 0,0015 m, avec un contact acier sur acier lubrifié μ = 0,12. On a d2 ≈ d = 10 mm = 0,01 m, soit au serrage :
- M1 = 0,00097×Ft
(Ft en N, M1 en Nm).
Adhérence de la tête de vis ou de l'écrou sur le plat ou le fraisage
[modifier | modifier le wikicode]Lors du serrage ou du desserrage, la partie que l'on manipule — tête de vis dans le cas d'un système vis/trou taraudé, tête de vis ou écrou dans le cas d'un boulon — frotte sur la partie plate de la pièce (ou sur la rondelle ou le joint), ou bien sur le fraisage (vis à tête fraisée). Nous prenons ici le cas d'un écrou.
Isolons l'écrou. La vis exerce une action dont la résultante est la force Ft. Il se crée donc une résistance au pivotement. Cette résistance se traduit par un couple résistant de moment M2 :
- M2 = μ×Ft×rt
où
- rt est un facteur de forme qui dépend de la forme de la tête de vis, une sorte de rayon moyen sous tête ;
- μ est le coefficient d'adhérence ; il peut être différent du coefficient d'adhérence sur le filet si les matériaux ou la lubrification sont différents.
Si la surface est un disque évidé de rayon intérieur rint et de rayon extérieur rext — par exemple vis à tête cylindrique, vis à tête hexagonale (il y a une collerette, portée circulaire située sous la tête), écrou hexagonal (il a des « bords relevés » donc une surface de contact circulaire), écrou à embase tronconique, écrou serré à la main (papillon, moleté, à croisillon) —, on a :
- .
Démonstration |
![]() On peut écrire la loi de Coulomb pour chaque élément de la surface de contact à la limite du glissement :
où
Cette force est tangentielle. Elle crée un moment résistant élémentaire
où r est la distance de la zone considérée à l'axe. Le moment total s'obtient en intégrant sur la surface de contact Σ :
On voit apparaître un facteur de forme (qui prend en compte l'aire et le moment d'ordre 1) rt, sorte de « rayon moyen sous tête » :
On a
![]() Pour calculer le moment d'ordre 1, on commence par intégrer sur un anneau compris entre les rayons r et r + dr, son aire vaut :
et donc
Donc : . |
Pour les diamètres extérieurs des têtes de vis et des écrous, voir la section Matage sous tête.
Dans le cas d'une vis ou d'un boulon, la largeur de la surface d'appui est faible devant son rayon, on a rext/rint ≈ 1, on peut donc faire l'approximation
- .
Démonstration |
On a les identités remarquables :
soit Comme rext ≈ rint, on a
|
Pour une tête hexagonale et un passage de vis de d + 1 mm, on a rt ≈ 0,64×d. Cette formule n'est valable que pour une forme de tête et un jeu de passage.
d | Formule utilisée | ||
---|---|---|---|
Formule exacte |
Moyenne (rext + rint)/2 |
Proportionnelle 0,64×d | |
M5 | 3,230 | 3,225 (-0,2 %) | 3,2 (-0,9 %) |
M6 | 3,994 | 3,975 (-0,5 %) | 3,84 (-3,9 %) |
M8 | 5,177 | 5,150 (-0,5 %) | 5,12 (-1,1 %) |
M10 | 6,442 | 6,400 (-0,7 %) | 6,4 (-0,7 %) |
M12 | 7,436 | 7,400 (-0,5 %) | 7,68 (+3,3 %) |
M16 | 9,939 | 9,875 (-0,6 %) | 10,24 (+3 %) |
M20 | 12,388 | 12,300 (-0,7 %) | 12,8 (+3,3 %) |
Si la surface est un tronc de cône de demi-angle au sommet α' — vis à tête fraisée (tête normalisée à α' = 45 °) —
- .
et donc
- .
Exemple
Considérons un écrou M10, avec un contact acier sur acier lubrifié, soit μ = 0,12. Le diamètre de la collerette sous tête vaut 14,6 mm, c'est aussi le diamètre du cercle inscrit dans l'hexagone ; donc rext = 14,6/2 = 7,3 mm. Admettons que la rondelle d'appui ait un diamètre intérieur de 12 mm : on a rint = 12/2 = 6 mm.
Nous avons donc :
- rt = 6,67 mm = 0,006,67 m
- M2 = 0,000,801×Ft
(Ft en N, M2 en Nm).
Relation complète
[modifier | modifier le wikicode]Le couple de serrage est la somme des moment calculés ci-dessus :
- C = M1 + M2
soit dans le cas d'une vis à filetage ISO à pas gros :
- C = (0,184×p + (0,577×d2 + rt)×μ)×Ft
et à l'inverse
Dans le cas de notre vis M10 :
- C = 0,001,77×Ft
(Ft en N, C en Nm). On voit que l'adhérence du filet représente 99 % du couple de serrage, et l'adhérence sous la tête représente 1 % de ce couple.
Résistance mécanique
[modifier | modifier le wikicode]Contrainte dans le filet
[modifier | modifier le wikicode]Le contact se faisant au niveau des dents celles-ci doivent supporter une contrainte qui peut être calculée.
Contrainte à la base de la tête de vis
[modifier | modifier le wikicode]Cisaillement
[modifier | modifier le wikicode]Il faut tenir compte des forces intérieures de cisaillement à la base de la tête de vis. Il est de bon ton de considérer les forces correspondant à la répartition des contraintes dans un cylindre de diamètre égal au diamètre à flanc de filet.
Bien que la vis ne doit pas avoir de contrainte de cisaillement, dans un assemblage la valeur de celle-ci est de 0,6 de la valeur de la rupture. (Dans un assemblage, des goupilles doivent être installées en cas de contrainte de cisaillement).
Cas du bois
[modifier | modifier le wikicode]Les vis à bois n'ayant pas un filetage suffisant pour travailler en traction, elles sont donc conçues pour travailler en cisaillement. Pour un assemblage en bois vissé travaillant en traction, il faut utiliser :
- des tire-fonds dont le filetage est adapté à ce genre de sollicitations
- Des inserts filetés pour utilisation avec des vis ISO standards
Références
[modifier | modifier le wikicode]- ↑ un flux bouclé est un ensemble d'efforts internes à un sous-ensemble rigide (classe d'équivalence cinématique), et indépendant des actions extérieures à ce sous-ensemble ; la somme de ces efforts est nécessairement nulle (condition d'équilibre), les vecteurs force mis bout à bout forment un polygone fermé, d'où cette notion de « boucle » et de « flux »
C. Teixido, J.-C. Jouanne, B. Bauwe, P. Chambraud, G. Ignatio et C. Guérin, Guide de construction mécanique, Delagrave, (ISBN 2-206-08224-1), p. 281 - ↑ Norme ISO 724 Filetages métriques ISO pour usages généraux - Dimensions de base.
- ↑ la classe de qualité est composée de deux nombres, sous la forme a.b ; la limite élastique en MPa vaut Re = 10 × a × b (pour une vis de classe 8.8, Re = 640 MPa)
- ↑ correspondant à 3⁄4 de la limite élastique (coefficient de sécurité de 1,3), filetage à pas gros, pour un montage graissé monté avec rondelles plates (coefficient de frottement μ = 0,12) ; André Chevalier, Guide du dessinateur industriel, Hachette, (ISBN 978-2-01-168831-6), p. 336
- ↑ correspondant à 3⁄4 de la limite élastique ; sections résistantes : Jean-Louis Fanchon, Guide des sciences et technologies industrielles, Nathan, (ISBN 978-2-09-161590-5), p. 194
- ↑ allemand Rudolf Kellermann et Hans-Christof Klein, « Untersuchungen über den Einfluß der Reibung auf Vorspannung und Anzugsmoment von Schraubenverbindungen », dans Konstruction, Springer Verlag, vol. 2, 1955 [texte intégral]
- ↑ op. cit., formule (17) p. 4
- ↑ John H. Bickford, Introduction to the Design and Behavior of Bolted Joints, Marcel Dekker, , 709 p.
- ↑ http://machinedesign.com/article/understanding-the-nut-factor-in-threaded-fastener-torque-tension-relationship-0818
- ↑ http://www.archetypejoint.com/?page_id=135
- ↑ Jean Guillot, « Modélisation et calcul des assemblages vissés. Généralités », dans Techniques de l'ingénieur, Éditions TI, no BM 5 560, 2007, p. 14
- ↑ Guillot, op. cit. p. 15
- ↑ normes ISO 4014 (vis) et ISO 4032 (écrous)
- ↑ norme ISO 4762
- ↑ normes EN 1665 (vis) et EN 1661 (écrou)
- ↑ 28,2 mm pour une tête de vis, 27,7 pour un écrou à embase
- ↑ Guillot, op. cit., p.16
- ↑ Guillot, op. cit., p.11
- ↑ Kellermann et Klein définissent un coefficient d'adhérence apparent
µ' = µ/cos(θ) soit tan(φ') = tan(φ)/cos(θ) ;
il leur vient
M1 = d2×Ft×tan(α + φ')
Liens externes
[modifier | modifier le wikicode]- Calcul liaison vissée
- Boulons – Capacités nominales
- allemand Publications sur le sujet (Kamax, entreprise fondée par Rudolf Kellermann)